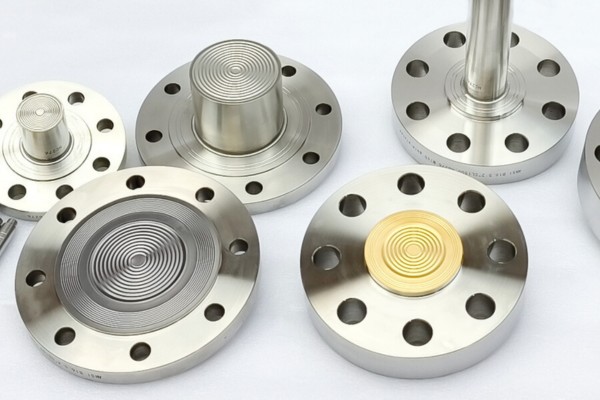
As the mechanical manufacturing and automation industries move towards high precision, high reliability, and intelligence, the harshness of the equipment operating environment and the refined needs of process control have put forward higher requirements for core components. As the "protective barrier" of the pressure sensing system, diaphragm seals have become the key technical support for ensuring the stable operation of equipment and intelligent manufacturing with their corrosion resistance, high-pressure resistance, and accurate signal transmission.
Industry Difficulties: Challenges of Pressure Monitoring
In mechanical manufacturing and automation scenarios, pressure sensors need to face the following challenges:
⒈ Medium erosion: Chemical substances such as cutting fluids and lubricating greases are prone to corrode sensor diaphragms, resulting in shortened equipment life;
⒉ Extreme working conditions: High temperature (>300℃) and high pressure (>50MPa) environments in processes such as casting and welding are prone to cause sensor failure;
⒊ Signal distortion: Viscous media (such as adhesives and slurries) or crystalline substances are prone to block sensor interfaces, affecting data collection accuracy.
These problems not only increase equipment maintenance costs but may also lead to production interruptions or product quality fluctuations due to deviations in monitoring data.
Technological breakthrough of diaphragm seals
Diaphragm seals provide double protection for pressure sensing systems through innovative design and material upgrades:
1. Corrosion resistance and high pressure resistance
■ Using Hastelloy, titanium, or PTFE coating technology it can resist corrosion from strong acids, strong alkalis, and organic solvents;
■ The welded sealing structure supports a temperature range of -70℃ to 450℃ and a high-pressure environment of 600MPa and is suitable for scenarios such as CNC machine tool hydraulic systems and injection molding units.
2. Accurate signal transmission
■ The ultra-thin metal diaphragm (thickness 0.05-0.1mm) realizes lossless pressure transmission with an accuracy error of ≤±0.1%;
■ The modular interface design (flange, thread, clamp) meets the complex installation requirements of industrial robot joint drives, automated pipelines, etc.
3. Intelligent adaptation
■ Integrated strain gauges monitor the sealing status in real time and realize fault warning and remote maintenance through the industrial Internet of Things platform;
■ The miniaturized design is suitable for precision scenarios such as collaborative robot joints and microfluidic control valves.
In the field of mechanical manufacturing and automation, diaphragm seals have evolved from single functional components to key nodes in the intelligent manufacturing system. Its technological breakthrough not only solves the pain points of traditional pressure monitoring but also provides a reliable foundation for the intelligent and unmanned upgrade of equipment.
WINNERS METALS provides high-performance, high-quality diaphragm seals, supporting customized production of SS316L, Hastelloy C276, titanium, and other materials. Please contact us for details.
Post time: Mar-14-2025